Overview of the 5 Types of Hazards Defined by Industrial Hygiene
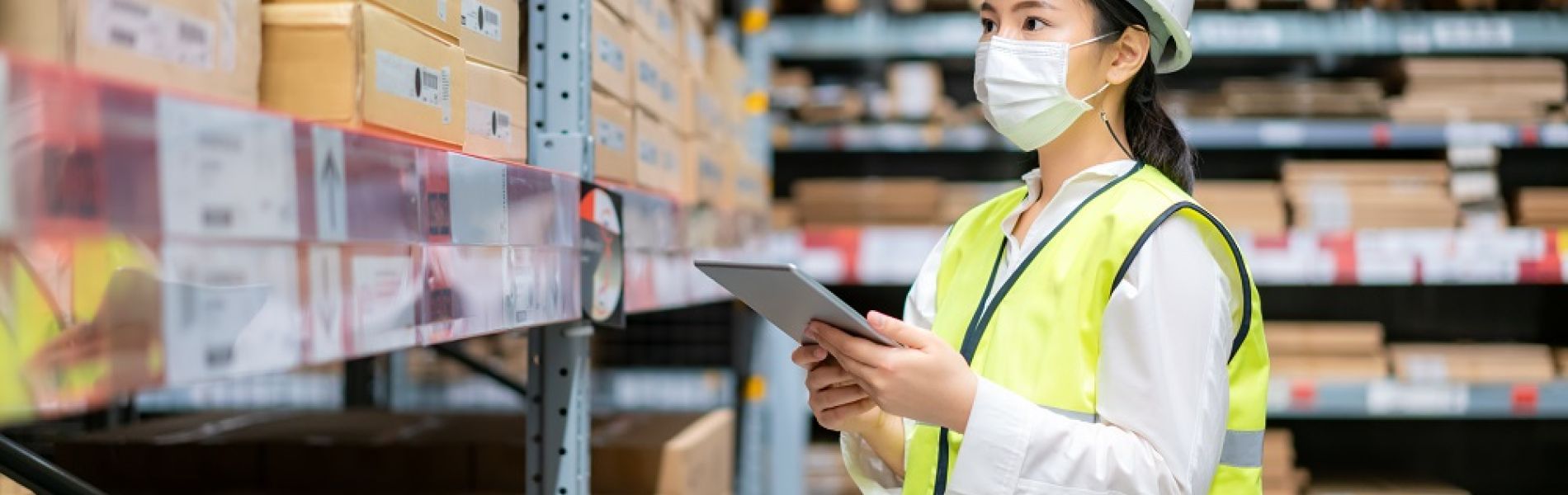
Industrial Hygiene is the science of recognizing and evaluating environmental hazards that could cause illnesses or other injuries. An industrial hygienist must assess risk based on both observed outcomes as well as anticipated ones.
The study and practice of industrial hygiene plays a vital role in the health and safety of workers across the globe. Governments and industries have developed standards over time that are meant to contribute to the welfare of those doing the work as well as the health and well-being of surrounding communities.
Within these standards are generally accepted categories of hazards. The types of hazards defined by industrial hygiene are: airborne hazards, chemical hazards, biological hazards, ergonomic hazards, and physical hazards.
We’ll break down each of these categories, and answer some common questions about industrial hygiene.
5 Types of Industrial Hygiene Hazards
Airborne hazards
Any task that produces particulates, gas, or vapor contaminants presents an airborne hazard. The most common air contaminants typically include:
- Dusts, or solid particulates that result from the physical alteration (crushing, grinding, burning, etc.) of materials such as rock, wood, metal, and grain.
- Fumes, the result of material that has become a vapor then cooled in the air to become suspended particulates.
- Mists, a vaporized material that has condensed back to a liquid state, or a liquid that has been dispersed into the air and broken into fine liquid droplets that remain suspended in the air for a period of time.
- Aerosols, especially fine liquid particles that easily enter the lungs.
- Fibers, a solid particle whose length is several times its diameter.
Chemical hazards
Chemical hazards present a risk to humans when they are inhaled, come in contact with the skin (corrosive injury), are absorbed through the skin, or are ingested. These hazards are found in the form of solids, liquids, gasses, mists, dusts, fumes, and vapors. Industrial hygiene standards typically take into account the concentration of the chemical present when assessing worker risk.
Biological hazards
These hazards include bacteria, viruses, fungi, and other living organisms. The risk from biological hazards presents when they enter the human body through breaks in the skin or through inhalation, absorption, or ingestion. Once inside the body, these organisms can cause acute or chronic infections. Biological hazards are most commonly found in settings where workers come in contact with organic and/or living organisms, such as those found in healthcare or food processing.
Ergonomic hazards
Ergonomics is the study of how people work within their environment. Ergonomic hazards are present when tasks involve motion or movement that puts undue strain on the body or places the body at risk of physical harm due to the motions involved in specific tasks. Repetitive motion tasks also pose a high risk for becoming ergonomic hazards.
Physical hazards
Physical hazards include excessive exposure to physical stimulants, such as noise, illumination, temperature, vibration, and both ionizing and nonionizing electromagnetic radiation. While radiation risks are not common across all industries, most other physical hazards can be present in a variety of work environments.
Common Questions About Industrial Hygiene
How do workplaces control hazards?
Across the field of health safety, professionals usually use the same types of controls to manage hazards. This includes industrial hygiene-related concerns.
- Engineering controls manage risk by isolating workers from the hazard or reducing/removing the hazard at the source. A dust collection unit in a wood shop is a type of engineering control.
- Workplace controls adjust the manner and space in which the tasks are performed to manage risk. For instance, isolating break rooms and meal areas and encouraging proper hand washing reduces the risk of ingesting chemical or biological hazards.
- Administrative controls include high-level tasks such as process management and scheduling. Properly managing risk at an administrative level adds another layer of protection against occupational hazards.
Who is responsible for health and safety in the workplace? Why are they responsible?
The answer to this question may vary in specifics from country to country, but it is almost universally agreed upon that it is incumbent upon the employer to manage health and safety in the workplace. The reason for this is that the employer, be it an organization or an individual, is the reason for workers engaging in the tasks they are doing. The employer should organize tasks in such a way that those workers carrying out the tasks are not at undue risk of encountering an occupational hazard.
The field of industrial hygiene exists to aid employers in ensuring the safety of their workforce. It is unlikely that the owner of a metal working shop knows everything there is to know about ergonomic hazards, but the nature of the tasks within the shop may be placing workers at risk. An assessment by an industrial hygienist can reduce both risks and costs by not having the overhead of paying for job-related injuries.
Are there any international organizations that set standards for workplace safety?
Most countries will have their own workplace safety organizations within their governmental framework, but there are several international organizations that work together to promote industrial hygiene knowledge and best practices worldwide. Here are a few:
- International Occupational Hygiene Association: “IOHA was established to improve, promote and develop occupational hygiene worldwide through its member organizations, and to improve and maintain a safe and healthy working environment for all.”
- International Commission on Occupational Health: “ICOH is an international non-governmental professional society whose aims are to foster the scientific progress, knowledge and development of occupational health and safety in all its aspects.”
- International Ergonomics Association: “The mission of the IEA is to elaborate and advance ergonomics science and practice, and to expand its scope of application and contribution to society to improve the quality of life, working closely with its constituent societies and related international organizations.”
For many business organizations, industrial hygiene is a global issue that requires a global solution. Contact Inogen Alliance for more information about our Industrial Hygiene Programs.
Inogen Alliance is a global network made up of dozens of independent local businesses and over 5,000 consultants around the world who can help make your project a success. Our Associates collaborate closely to serve multinational corporations, government agencies, and nonprofit organizations, and we share knowledge and industry experience to provide the highest quality service to our clients. Learn more about how you can work with Inogen Alliance by exploring our Associates or Contact Us. Watch for more News & Blog updates here and follow us on LinkedIn.